eMax has always focused on material joining processes and techniques. Together with the following partner companies we provide industry leading equipment and support. |
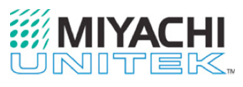
Laser Welding Equipment: Fiber Lasers, Nd:YAG Laser welding is a non-contact process which requires access to the weld zone from only one side of the parts being welded. The laser weld is formed as the intense laser light rapidly heats the material - typically calculated in milliseconds.
As laser welding is a non-contact process, there are a great number of joint geometries that can be welded. The most significant requirement is that there is a close fit-up at the joint interfaces. Laser welders can join a wide range of steels, nickel alloys, titanium, aluminum, and copper. As with other joining technologies, some materials are difficult to laser weld unless they meet specific characteristics, namely, reflectivity, the effect of high thermal cycles, and the vaporization of volatile alloying elements. |
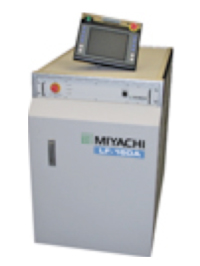 |
Laser Marking & Laser Engraving Equipment: Fiber Lasers, Nd:YVO4
A fast and clean technology, laser marking (also known as laser engraving or laser etching) is rapidly replacing older marking methods. A key factor in this widespread adoption is the exponential increase in the use of direct marking of part information to enable tracking and traceability across many industries, most notably medical device and automotive electronics manufacturing. Easy and flexible automation, improved environmental profile, and low cost of ownership add to the benefits of laser marking equipment or laser etching equipment. Miyachi Unitek's complete laser marking equipment product offering includes Fiber, Nd:YV04, and 'Green' (frequency doubled/532nm) laser markers. UV and CO2 laser markers are also available for integration into systems. |
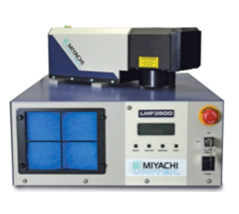 |
Laser Systems - Welding, Cutting, Marking & Engraving
Miyachi Unitek offers a complete range of turn-key semi-automated systems for laser welding, laser cutting, laser marking & laser engraving, providing the fastest path from application concept to full production.
Miyachi Unitek not only manufactures laser welders and laser markers, but also engineers and integrates laser systems, offering designers a one-stop shop for system integration. This includes running samples of the process in-house to ensure it does the entire job as specified, and answering in-depth application questions. |
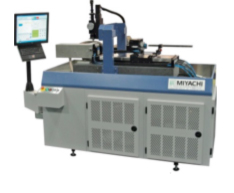 |
Resistance Spot Welding Power Supplies
Resistance Welding - also known as "spot welding" - is a thermo-electric process in which heat is generated at the interface of the metal parts to be joined by passing an electrical current through them for a precisely controlled time under controlled pressure.
Miyachi Unitek offers a complete line of resistance welding power supply technologies including Linear DC, Inverter, AC, and Capacitive Discharge. A typical bench top system would include a resistance welding power supply, a resistance welding head, and a weld monitor. |
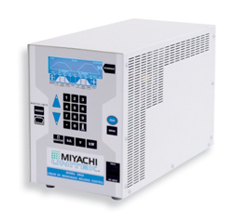 |
Resistance Welding Heads
Miyachi Unitek offers a full range of resistance welding heads including manual, air-actuated, and electromagnetic models with opposed, step, series, and parallel gap electrode configurations. Force ranges from just .08lbs (40g) to 1600lbs (725.7kg) to address both fine and large scale spot welding applications. |
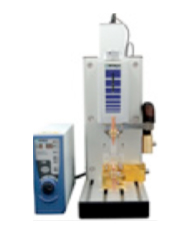 |
Resistance Welding Monitors & Checkers
Real time weld monitors - also called weld checkers - are invaluable tools for production monitoring, process development and weld quality analysis. Weld monitors measure one or more of the electrical and/or mechanical parameters that dynamically change during the welding process including weld current, voltage drop across the electrodes, work piece expansion and deformation, electrode force, electrode displacement (movement) and more.
Miyachi Unitek offers a full range of desktop, hand-held and machine-mountable weld monitors / weld checkers, some with built-in printers or RS232 output. |
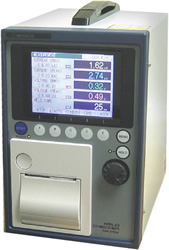 |
Reflow Soldering/Bonding Equipment
Hot Bar Reflow Soldering is a selective soldering process where two pre-fluxed, solder or adhesive coated parts are heated to a temperature sufficient to cause the solder or adhesive to melt, flow, and solidify, forming a permanent electro-mechanical bond between the parts. Typical hot bar reflow soldering applications include flex circuits, ribbon cables, wires, flex to PCB, flex to LCD, and thermo compression bonding of gold ribbon as found in the telecommunications, computer, automotive, display industries and more.
Miyachi Unitek offers a full range of products for hot bar reflow soldering including reflow soldering power supplies, thermodes, reflow bonding heads, and both single operator desktop systems and standalone systems such as those used for flat panel display repair. |
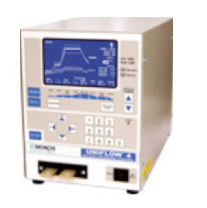 |
Ultrasonic Welding 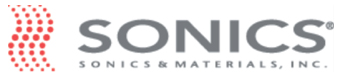
Sonics & Materials, Inc. has been a world leader in the field of ultrasonic welding since 1969, and is an ISO-9001 certified manufacturer of a complete line of ultrasonic metal welding systems and equipment for bonding conductive materials in applications such as wire splicing, wire termination, battery tabbing, cable processing, seam welding and tube sealing. Sonics' ultrasonic metal welding systems include spot welders, seam welders, and wire splicers, and custom fixturing and tooling is also provided. |
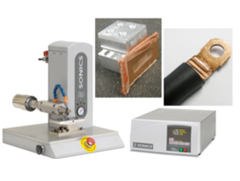 |
Wire Bonding 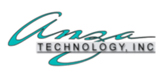
AnzaTechnology has over twenty five years of designing, building, and selling state of the art Ultra-sonic Wire Bonders (Ball/Wedge/Tab), Die Bonders, Shear and Pull Testers, and ESD Precision Tools.
Anza manufacturers a full-line of tabletop manual, semi-automatic, and fully-automated bonders and testers that are cost-effective machines for low to medium volume production. |
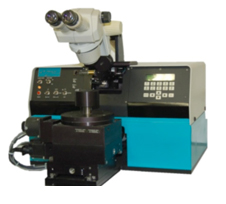 |
Fume Extraction 
Fumex, Inc. has been a worldwide leader in the design and manufacture of quality fume extraction systems as well as commercial and industrial air filtration systems for over 25 years. Modern manufacturing processes often require the use of materials that disseminate noxious or toxic gas fumes, vapors and odors into the workplace. Our focus is to provide equipment that captures these pollutants at the source, ensuring workplace health. Fumex industrial air filters, fume extractors and dust collectors have proven their value in many situations. Some uses of our fume extraction and dust collection systems are:
Removal of:
• Printing Fumes
• Welding Fumes
• Laser Fumes
• Soldering Fumes
• Dental Lab Dust
• Industrial Odor Removal
• Food & Beverage Manufacturing
• Pharmaceutical Manufacturing
• Electronics Manufacturing
|
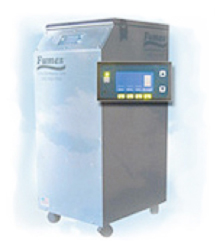 |
|
|
|